Types of Hot Melts & Polyurethane Reactives
Polyolefins Based
Hot Melt Adhesives (HMA) come in the form of glue sticks, granules and brick shapes that require heating elements like glue guns or heated tanks to melt flow these thermoplastic-based compounds for use. For industrial application, these HMA will provide a fast-setting property that yields good adhesion strength for lightweight materials like paper, wood, cork and many types of plastics. It is widely used in the industrial segment for electronic components rigidisation, HEPA filter media assembly, edgebanding, bookbinding, corrugated packaging and many more applications that require simple, fast, solvent-free adhesive bonding.

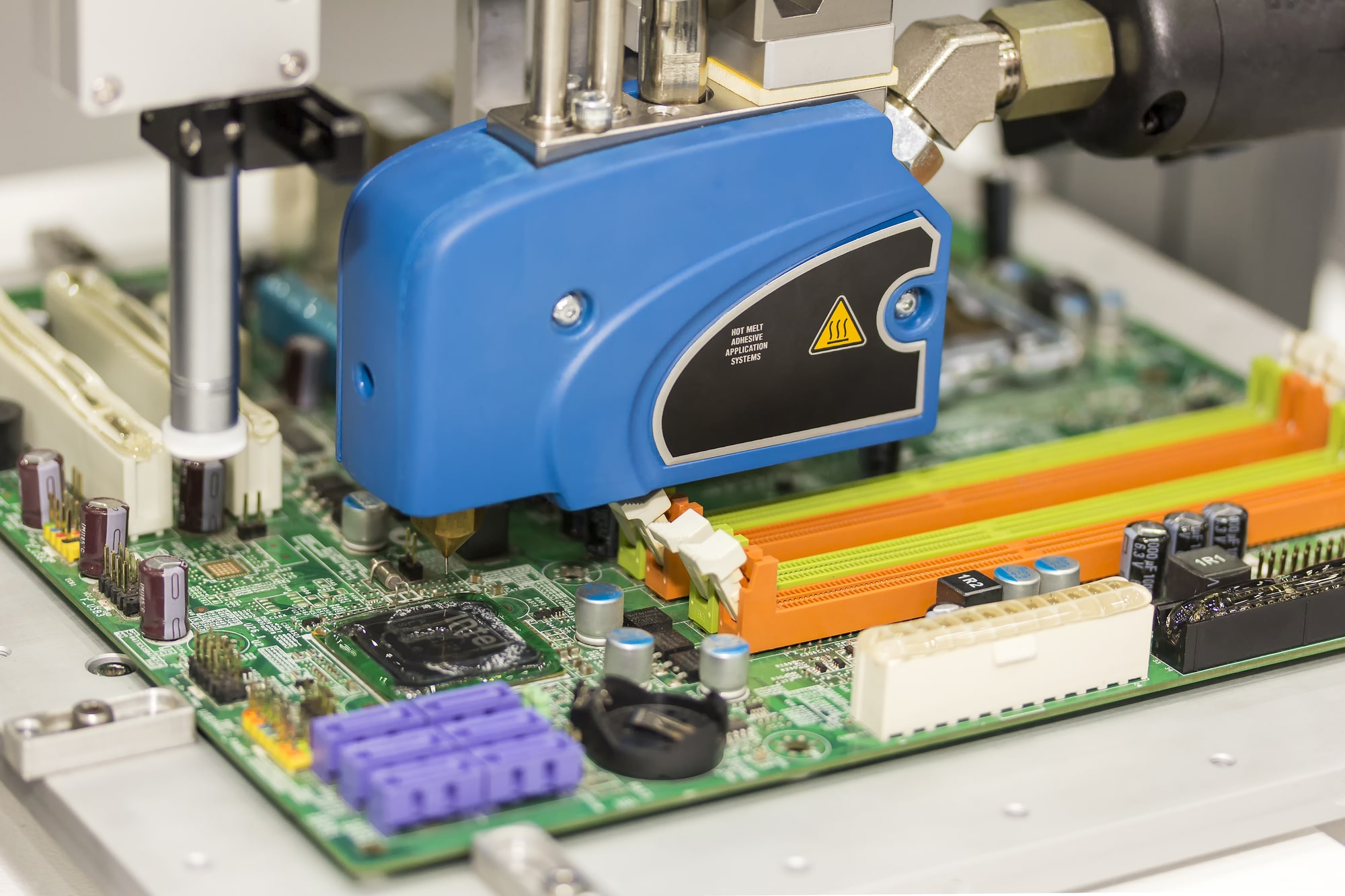
Polyurethane Reactive Adhesives
Polyurethane Reactive (PUR) hot melt has a combination of different positive attributes found in various, unique adhesives. PUR hot melt is not found in the normal form of a glue stick or bulk pellet, instead, it is melted from a solid prior to application and commonly dispensed from a 10oz tube similar to caulking adhesive or from a standard airtight 20 Kg drum.
PUR hot melt solidifies through moisture in the air to form a super strong bond that will not re-melt. There are both high and low-temperature PUR adhesives so the correct PUR applicator must be used. The reaction time is mostly between 24 to 72 hours. The reaction time must not be confused with the fast setting time with hot melts, in general, are known for. A PUR hot melt still can have a fast setting time from several seconds to minutes but it takes a longer time to set.
Because polyurethane is so strong and durable, it is ideal for a wide variety of applications. PUR is often used in woodworking and many other applications that would require a super stronghold with a very fast set time. PUR sets within five seconds, and will not re-melt.
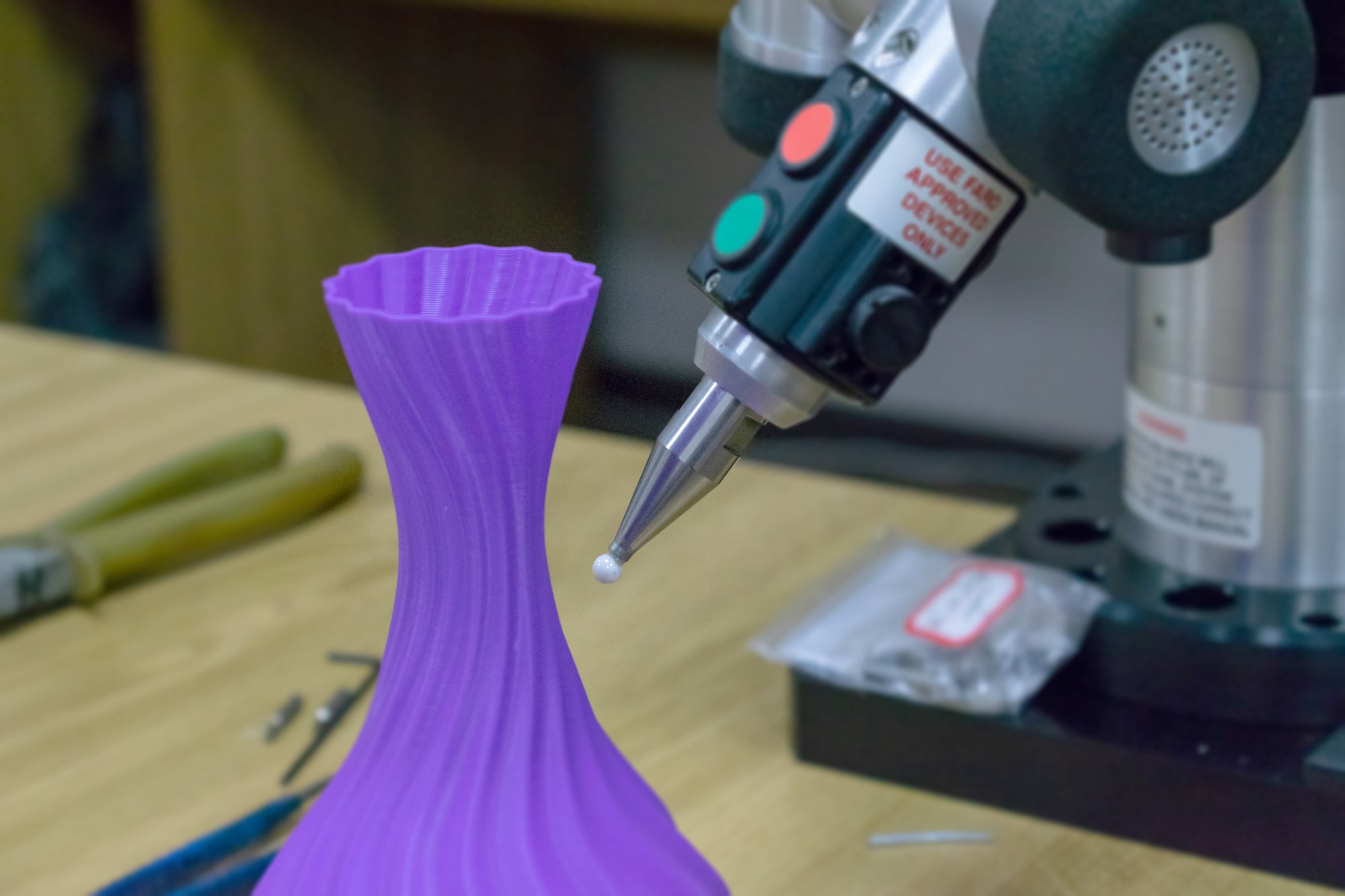
Properties of Polyurethane Adhesive
Polyurethane Reactive (PUR) is a versatile adhesive that reacts with moisture for polymerisation to form a strong bond between the different types of substrates. As this is a thermoset-based compound, once set it will fully cross-linked to form a tough and structural adhesive that gives very high adhesion strength that not only resists water but also has thermal and impacts resistance. Being a 1 component adhesive, it will melt flow at the right temperature and set rapidly upon contact between bonding substrates without any release of volatile organic compounds.
Frequently Asked Questions
-
Open Time is the timing required for the molten hot melt in liquid starts to solidify. Generally, it will take anything between 3 - 40 seconds and it is largely depending on the formulation of the hot melt adhesive.
-
Setting Time is the timing required for the molten hot melt to set and hold the 2 mating parts together the moment it is contacted.
- Stick form
- Granule shape
- Pallet shape
- Mini pillow shape
- Block form
Yes. It is 100% thermoplastic and will not set and polymerise like thermoset type of adhesives.
It ranges between 600C to 1400C depending on the base of the hot melt being selected. For EVA based hot melt, the highest temperature it can withstand is up to 700C whereas for Polyamide hot melt, it can heat up to 1400C.
Hot melt is made of thermoplastic and with the higher melting temperature, the viscosity will decrease drastically. The opposite will happen if the melting temperature is lower than recommended.
Polyurethane hot melt usually does provide a stronger bond than a traditional hot melt. This is because the PUR hot melt forms a strong initial bond and then continues to strengthen as the adhesive reacts with moisture in the air. This is a chemical process known as cross-linking where the PUR hot melt attaches to the object being glued and itself to form a strong, permanent bond.
The answer is the air and the object being glued. There is plenty of moisture in the air to continue curing PUR hot melt; however, drier conditions may extend open times.
If unopened, the adhesive should be stored in a foil pouch in a cool, dry location. Do not expose the PUR tube to rain or moisture. Before shutting down for the day, extrude a one-inch bead of adhesive to ensure that air has been extracted from the tube. CAUTION: Do not touch the applicator heat cylinder or cartridge when at maximum temperature. Always wear gloves.