CONDUCTIVE ADHESIVES
Conductive Paste, Film & Wafer Dicing Tape
Die Attach Epoxy Paste
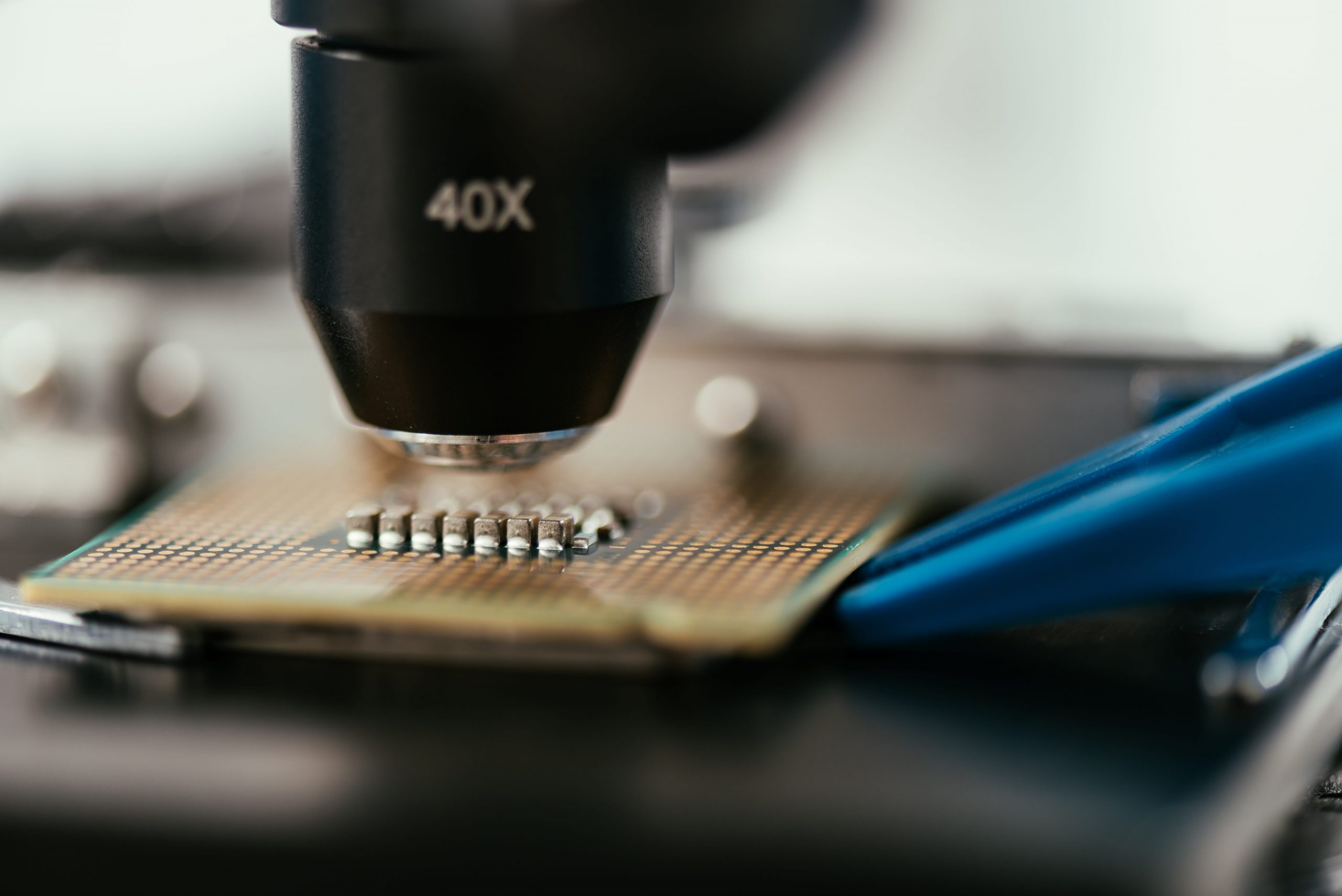
Die Attach Film (DAF)
Die-Attach film (DAF) adhesive has become popular and mandatory when stack chips are used to accomplish larger capacity in 3-D packaging of flash memory devices. The push now is for even thinner insulating die-attach adhesive that can properly handle interfacial stresses in stacking chips with bond-lines as thin as 8-10 microns or less to help mobile devices to achieve even lower profiles.
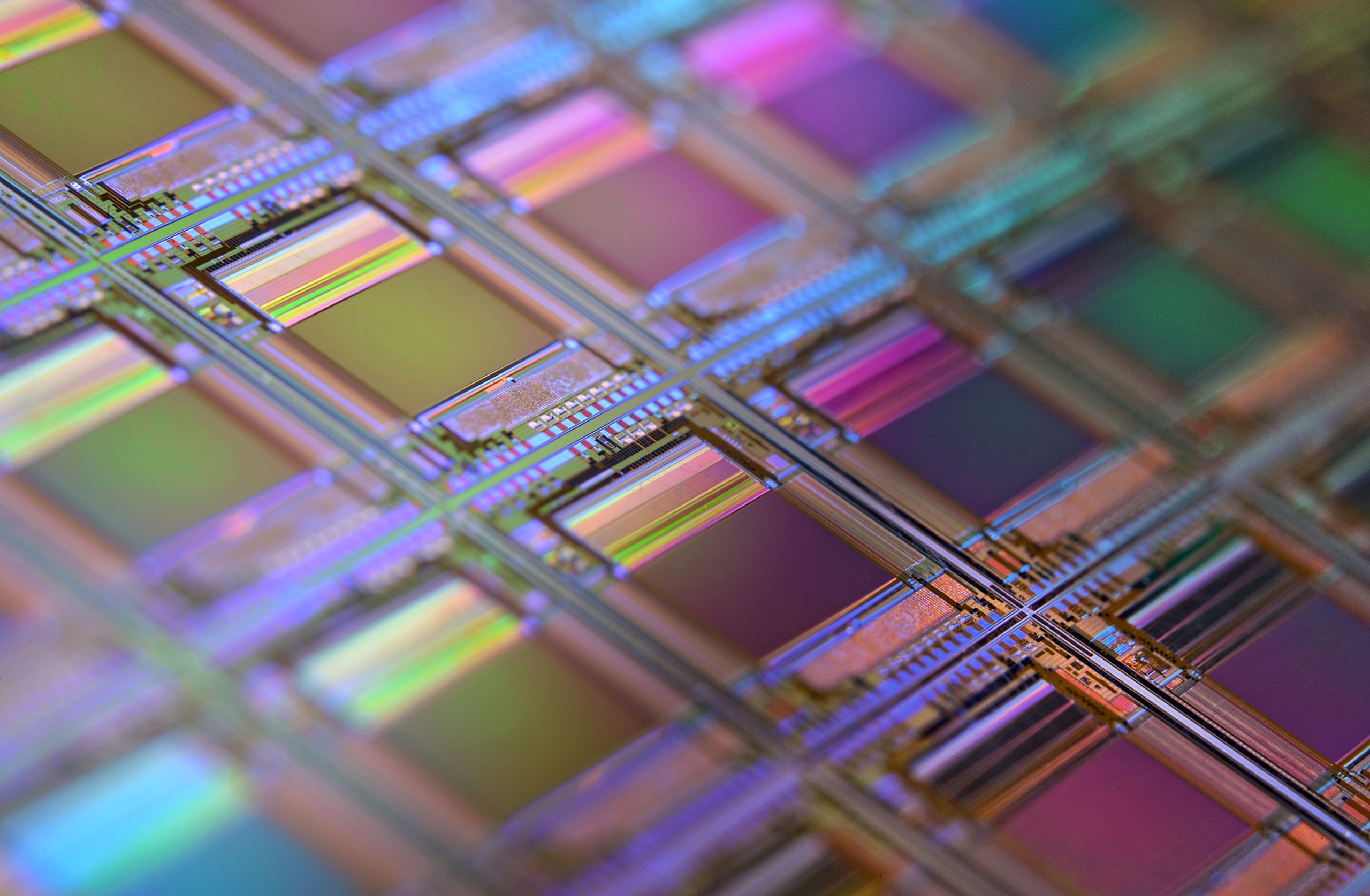
Dicing Die Attach Film (DDAF)
AI Technology, Inc. is the only US company that is well known to manufacture its own dicing tapes for wafer dicing in the United States since 2005. While AIT manufactures more traditional controlled peel, UV and heat induced releasing dicing and grinding tapes, one of its pioneering technologies in the controlled peel strength dicing tape application is the availability of tapes that withstand high temperature exposure up to 250°C.
The compatibility of the dicing tapes with the DAF adhesive must be tested and proven before adoption. In this application of dicing tape with die-attach adhesive there are two basic criteria beyond the traditional characteristics:
- It must have good bonding to the DAF and yet can be released without causing part of the DAF to be delaminated from the diced chips.
- The DAF must be free of residuals after the dicing tape is removed.
In addition to not leaving residuals on the DAF on the diced chip, AIT dicing tapes designed for the DDAF application are engineered to blend and form part of the DAF during curing to eliminate all fear of contamination induced failure.
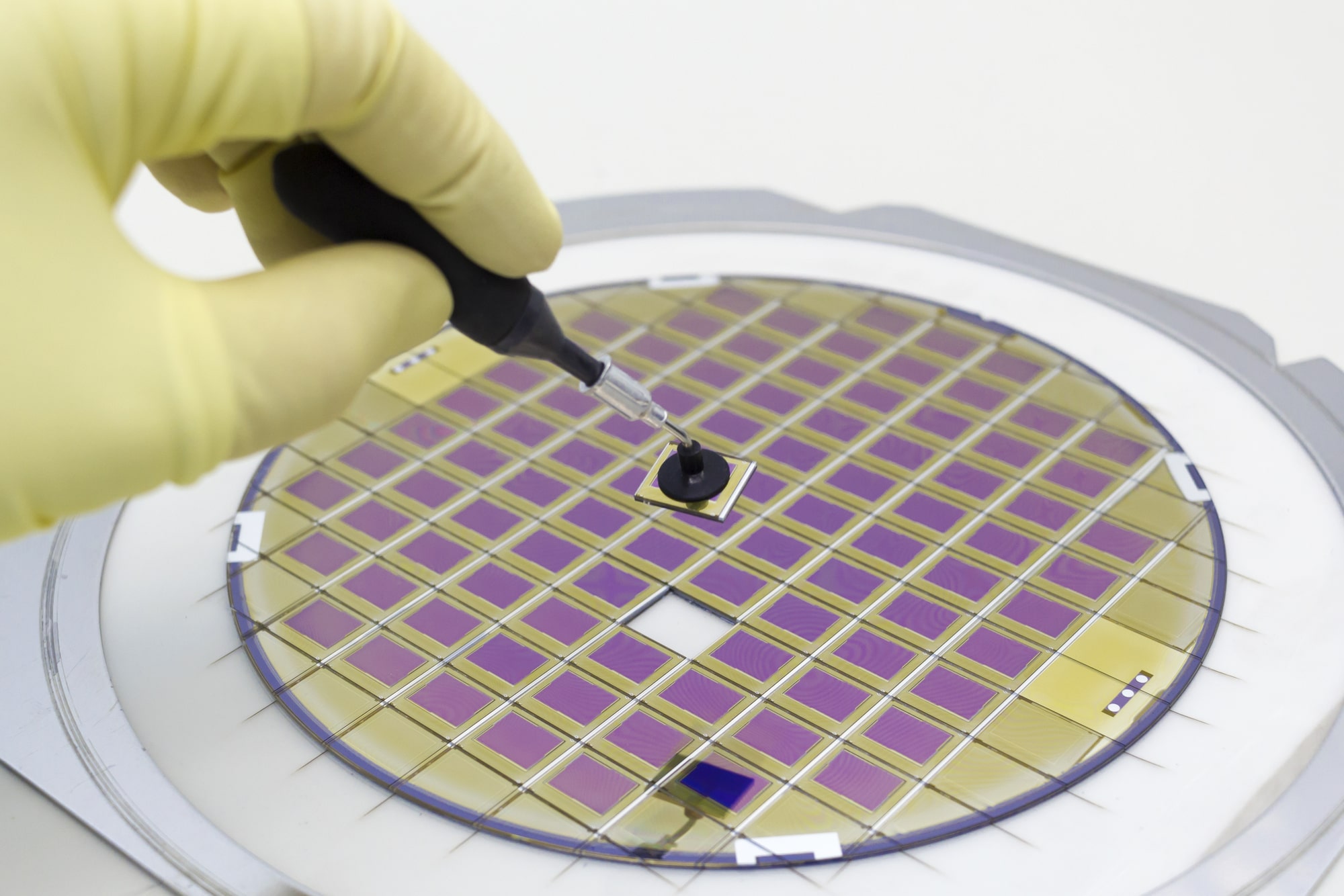
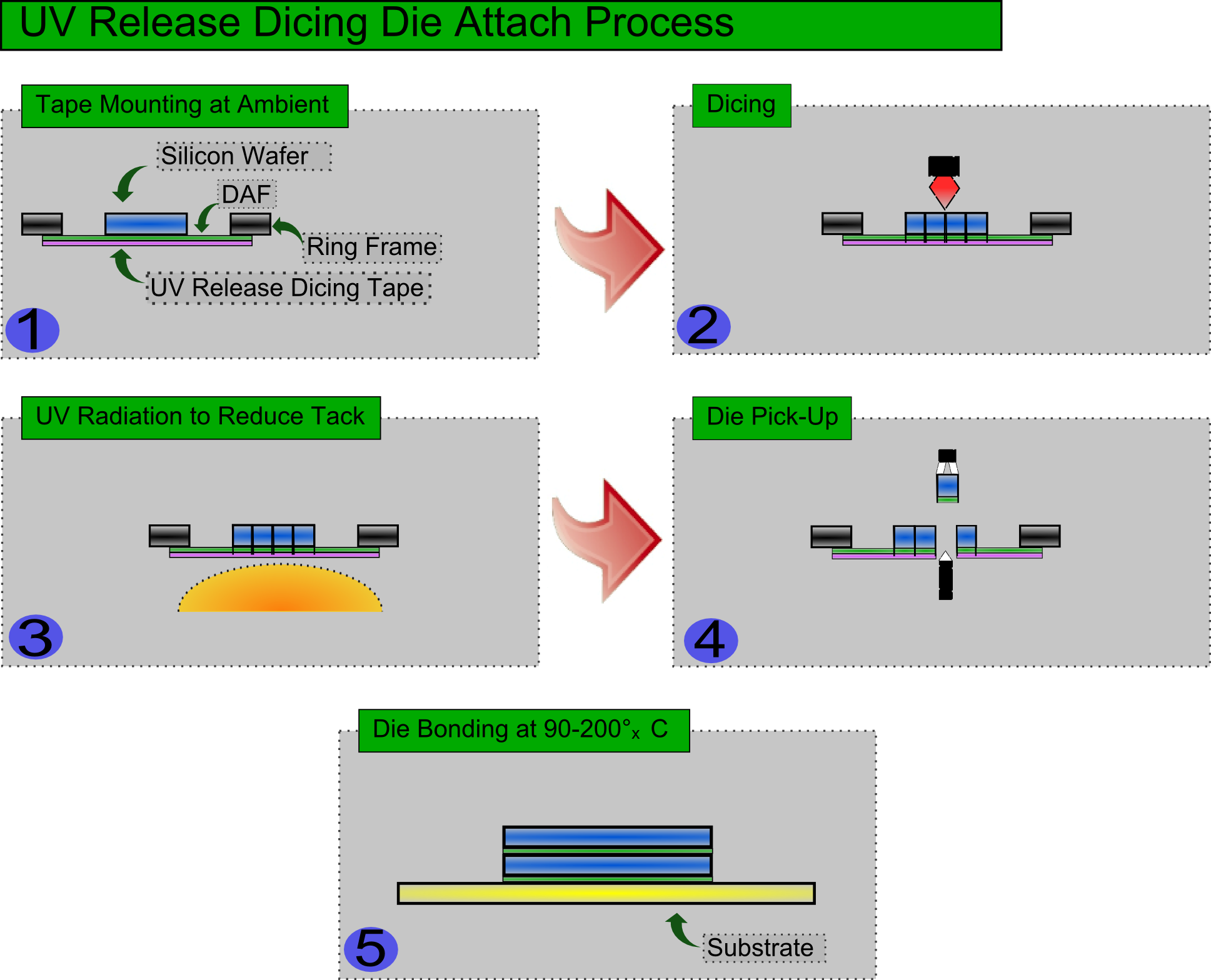